Our Services
Shree Ashapura Moulds is a well-established and respected manufacturer based in Ahmedabad, India, specializing in PET preform moulds. Our company is known for its advanced PET molding technologies, offering professional solutions tailored to your specific needs. With an experienced design and technical team, we are fully equipped to assist you in setting up a new PET molding line or enhancing existing pet mold technologies. We welcome you to reach out to us for comprehensive technical support and guidance regarding PET moldings.
We provide the following services:
PET bottle manufacturing using injection molding involves several steps. Here is an overview of the process:
- Raw Material Preparation: The primary material used in PET bottle production is polyethylene terephthalate (PET) resin. The resin is typically in the form of small pellets. It is carefully selected and pre-dried to eliminate moisture, ensuring high-quality finished products.
- Mold Design and Preparation: A mold is designed based on the desired bottle shape and size. The mold consists of two halves, an injection side, and a blow side. The mold cavities are precision-machined to create the desired bottle shape.
- Injection Molding: The pre-dried PET resin is fed into an injection molding machine. The resin is heated and melted to a specific temperature, forming a molten PET material. The molten PET is injected under high pressure into the mold cavity through a nozzle and runner system.
- Cooling and Solidification: Once the molten PET is injected into the mold cavity, it rapidly cools down and solidifies, taking the shape of the mold cavity. Cooling is facilitated by circulating cool water or air through the mold.
- Mold Opening: After the PET has solidified and cooled, the mold is opened, separating the two halves. The injection side of the mold contains the solidified PET preform, which has a hollow interior.
- Preform Ejection: The solidified PET preform is ejected from the injection side of the mold using ejector pins or other mechanisms. The preform is then transferred to the blow side of the mold for the next stage of the process.
- Stretch Blow Molding: In the blow side of the mold, the preform is reheated to a specific temperature. It is then clamped into position and a stretching rod is inserted into the preform, stretching it lengthwise. Simultaneously, high-pressure air is blown into the preform, expanding it against the mold cavity walls, forming the final bottle shape.
- Cooling and Release: The blown bottle is cooled to set its shape and improve its structural integrity. The mold is opened, and the finished PET bottle is released from the mold cavity.
- Trimming and Quality Control: Any excess material or flash around the bottle neck is trimmed off. The bottles undergo rigorous quality control checks to ensure dimensional accuracy, wall thickness, and overall quality.
- Packaging and Distribution: The PET bottles are then packaged, labeled, and prepared for distribution to various industries such as food and beverage, cosmetics, pharmaceuticals, and more.
Injection molding is a highly efficient and widely used manufacturing process for producing PET bottles. It enables the production of bottles with consistent quality, precise dimensions, and high production volumes.
Preform Moulding
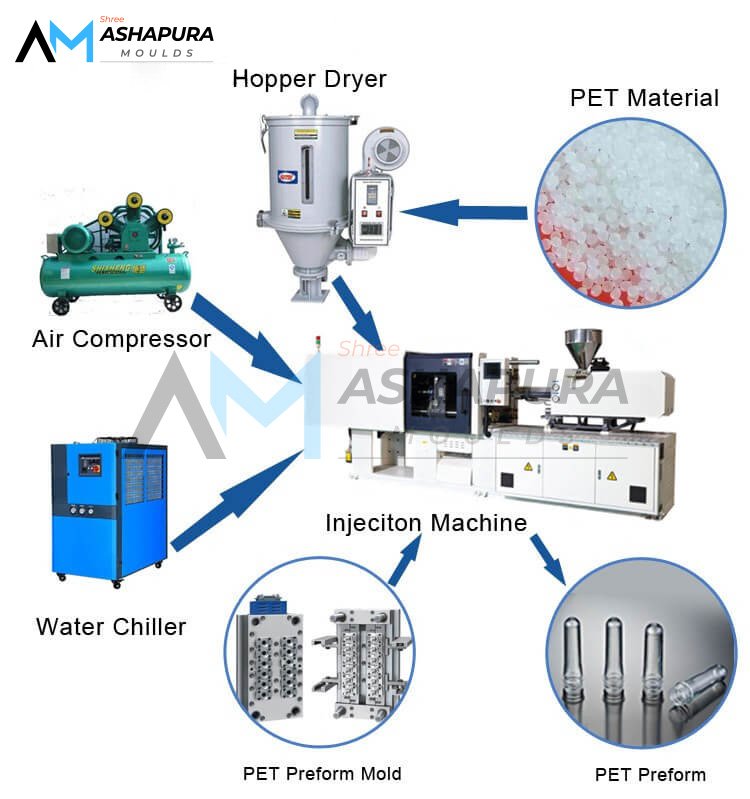
PET Preform Moulding Process
In the process of PET preform moulding, several key components and equipment play vital roles. Let’s delve into the significance of each:
- Hopper Dryer: A hopper dryer is used to remove moisture from the PET material before it is processed. Moisture can adversely affect the quality of the final preforms, so a hopper dryer helps maintain the desired moisture content for optimal results.
- PET Material: PET (polyethylene terephthalate) is a thermoplastic polymer widely used for manufacturing bottles and containers. It is lightweight, transparent, and has excellent barrier properties, making it suitable for various applications.
- Air Compressor: An air compressor supplies compressed air to the injection molding machine. Compressed air is required for various functions like ejecting preforms from the mould and cooling them rapidly.
- Injection Molding: Injection molding is the process by which molten PET material is injected into a preform mould cavity. The mould, typically made from steel, is designed to shape the material into the desired preform form. Injection molding machines provide the necessary pressure and temperature control to achieve precise and consistent preform production.
- Water Chiller: A water chiller is employed to cool down the moulds and maintain their temperature during the injection molding process. Cooling is crucial to solidify the molten PET material rapidly, allowing for efficient cycle times and preventing deformation.
- PET Preform Mould: The PET preform mould is a critical tool used to shape the molten PET material into preform forms. Shree Ashapura Moulds specializes in manufacturing high-quality PET preform moulds that are durable, precise, and tailored to specific customer requirements.
- PET Preform: PET preforms are the initial forms of the final bottles or containers. These preforms are produced through injection molding and typically have a threaded neck, allowing for easy attachment of caps or closures. PET preforms are subsequently reheated and stretched in the stretch blow molding process to create the final bottle shape.
Shree Ashapura Moulds, as a leading manufacturer of PET preform moulds, understands the importance of these components and equipment in ensuring efficient and reliable PET preform production. Their expertise lies in delivering top-notch moulds that contribute to the overall quality and success of the PET packaging industry.
Blow Moulding

PET Stretch Blow Moulding Process using Shree Ashapura Moulds’ Preforms
Shree Ashapura Moulds is a renowned manufacturer of PET preform moulds and is known for its expertise in the field of PET stretch blow molding. Their machines are designed to deliver high-quality and efficient production of PET bottles and containers. Here are the steps involved in PET stretch blow molding using Shree Ashapura Moulds’ Preforms:
- Preform Loading: PET preforms, which are produced through injection molding, are carefully loaded into the preform feeding system of Shree Ashapura Moulds’ stretch blow molding machines. The loading process can be done manually or automatically using a preform hopper or container.
- Preform Heating: The preforms are then transferred to the preform heating section of the machine. Shree Ashapura Moulds utilizes advanced heating technology, such as infrared heaters or ovens, to ensure precise and uniform heating of the preforms. This controlled heating process ensures optimal material characteristics for stretching and blowing.
- Preform Stretching: Once the preforms reach the required temperature, they move to the stretch station. Shree Ashapura Moulds’ machines employ sophisticated stretching mechanisms that allow for simultaneous stretching in both axial and circumferential directions. This stretching process enhances the strength, clarity, and overall quality of the final bottles.
- Preform Blowing: After stretching, the preforms are directed to the blowing station. Shree Ashapura Moulds’ machines utilize advanced technology to deliver precise and controlled injection of compressed air into the preforms. This ensures uniform expansion and accurate replication of the mold cavity, resulting in consistent bottle shapes and dimensions.
- Bottle Ejection: Once the blowing process is complete, the bottles are released from the mold cavity. Shree Ashapura Moulds’ machines incorporate efficient ejection systems that facilitate the smooth and reliable removal of bottles from the molds. This minimizes downtime and increases productivity.
- Cooling: The newly formed bottles may undergo a cooling process to stabilize their shape and enhance their dimensional accuracy. Shree Ashapura Moulds offers cooling solutions tailored to specific customer requirements, including air cooling or water cooling methods. These cooling systems ensure efficient and consistent cooling for optimal bottle quality.
- Quality Control: Shree Ashapura Moulds emphasizes stringent quality control measures. The bottles produced undergo comprehensive inspections and testing, including visual checks, dimensional measurements, and functional tests. This commitment to quality ensures that the bottles meet the highest standards and customer expectations.
- Bottle Collection: The final bottles are collected and prepared for further processing or packaging. Shree Ashapura Moulds’ machines can be seamlessly integrated with conveyor systems and other downstream equipment to facilitate smooth bottle collection, sorting, labeling, filling, capping, and packaging processes.
Shree Ashapura Moulds, with its expertise in PET preform moulds preforms, provides reliable and efficient solutions for the production of high-quality PET bottles and containers. Their commitment to innovation, precision, and customer satisfaction has established them as a trusted partner in the PET packaging industry.
Insightful!